Tänapäeval laaditakse enamikku laserlõigatud õhukesi plaate peamiselt käsitsi tõstmise teel, kusjuures 3 m pikkuste, 1,5 m laiuste ja 3 mm paksuste plaatide tõstmiseks on vaja vähemalt kolme inimest. Viimastel aastatel on edendatud käsitsi abistatavaid söötmismehhanisme, mis üldiselt kasutavad tõstemehhanismi + elektrilist tõstukit + vaakum-iminappade süsteemi söötmiseks. Siin analüüsitakse lühidalt vaakum-iminappade põhimõtet ja ettevaatusabinõusid, lootes, et rohkem lehtmetalli kasutajaid saavad sellest teadmisest aru.
Vaakum-iminappade rõhuprintsiip
Vaakum-iminapad imevad ja haaravad lehtmetalli vaakumrõhu abil. Plaadi pind on suhteliselt tasane ja iminapa serv on suhteliselt pehme ja õhuke, mis võimaldab plaadi külge kleepumist. Vaakumpumba kasutamisel tekib iminapa sisemisse õõnsusse vaakum, mis moodustab negatiivse vaakumrõhu. Vaakum-iminapa imemisjõud on proportsionaalne rõhu (vaakumi aste, rõhu erinevus iminapa sise- ja välispinna vahel) ja iminapa pindalaga, st mida kõrgem on vaakumi aste, seda suurem on imemisjõud; mida suurem on iminapa suurus, seda suurem on imemisjõud.
Dünaamiline imemisohutus
Välismaiste professionaalsete vaakumfirmade testitud andmete kohaselt peab tavapäraste elektritõstukite tekitatud vaakumrõhu ohutustegur olema kaks korda suurem. Ohutuse tagamiseks arvutab meie ettevõte iminapa teoreetilise imemisjõu ja määrab ohutu vaakumrõhu 60% vaakumi tingimustes ning jagab selle seejärel kahega, et saada vajalik ohutu imemisjõud.
Iminapa ja lehe seisukorra mõju tegelikule imemisjõule
1. Iminapa serva pinda (taldriku külge kinnitatavat külge) on vaja regulaarselt puhastada ja iminappa kriimustuste, pragude ja vananemise suhtes regulaarselt kontrollida. Vajadusel tuleb iminapp kohe uue vastu vahetada. Tegelikult kasutavad paljud ettevõtted ohtlikke ja ohutusriske kujutavaid iminappe.
2. Kui plaadi pind on tugevalt roostes ja ebaühtlane, tuleks ohutustegurit suurendada, vastasel juhul ei pruugi see kindlalt imada. Sellele olukorrale reageerimiseks on meie ettevõte uuenduslikult rakendanud kiirkonksusüsteemi, millel on 4 komplekti sümmeetriliselt integreeritud risttala mõlemasse otsa. Süsteemi rakendatakse kahel juhul: ① ootamatu voolukatkestus etteandeprotsessi ajal, teemantkonksu kasutamine ja plaat ei kuku maha. Materjal laaditakse uuesti, kui toide on sisse lülitatud; ② Kui plaat on roostes või paksus ületab 10 mm, kasutage esmalt iminappa, et seda veidi tõsta, ja seejärel kinnitage teemantkonks, et tagada ohutus ja ohutus.
Vaakumjõuallika mõju vaakumrõhule
Vaakum-iminapaga söötmine on käsitsi abistatav söötmismeetod, mis peab tagama personali ohutuse. Vaakumgeneraatori vaakumiaste on madalam kui vaakumpumbal, seega kasutatakse vaakumpumpa tavaliselt vaakumrõhuallikana, mis on ohutum. Professionaalsed söötmissüsteemide ettevõtted ei kasuta vaakumgeneraatoreid ja teine tegur on tingitud kõrgsurvegaasi vajadusest. Mõnes tehases on ebapiisavad või ebastabiilsed gaasiallikad ning gaasitorude paigutus on samuti ebamugav.
Vaakumpumpasid on kahte tüüpi. Üks neist kasutab kolme-/kahefaasilist elektrit ja tuleb ühendada töökoja elektrikilbist vaakum-imemissüsteemi juhtkilbiga. Kui kliendi kohapealne koormus on liiga suur ja aku ühendamine pole mugav, saab kasutada membraanpumpa ja 12 V akut ning akut regulaarselt laadida.
Eeltoodud tegeliku olukorra põhjal võime kokku võtta järgmised järeldused: ① Vaakum-iminapa meetod laserlõikamiseks ja -söötmiseks on ohutu, kui valitakse õige konfiguratsioon ja kasutus; ② Mida väiksem on plaadi värisemine, seda ohutum see on. Palun valige vaakumrobotkäsi, mis vähendab värisemist; ③ Mida halvem on plaadi pinnakvaliteet, seda vähem on selle imamiskindlus. Palun valige kõrge ohutuskonfiguratsiooniga vaakummanipulaator; ④ Iminapp on pragunenud või serva pind on liiga määrdunud ja seda ei saa kindlalt imeda. Palun pöörake tähelepanu kontrollile. ⑤ Vaakumjõuallika vaakumiaste on oluline tegur, mis määrab vaakumrõhu, ja vaakumpumba vaakumi tekitamise viis on ohutum.
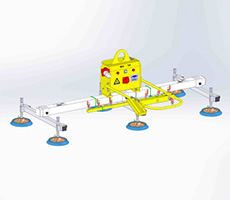

Postituse aeg: 20. aprill 2023